
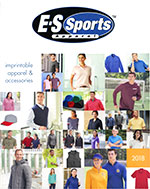
Alphabroder|Prime also used Pacejet to automate their shipping processes, which amounted to twice as fast workflows and double the number of shipments each day. They also reduced their workstations because each station now executed all shipping processes instead of relying on specialized stations throughout each location.
Alpha broder software#
In addition to averting a crisis, alphabroder|Prime also experienced a return on investment as they no longer need separate software licenses, shipping portals, and data integrations.
Alpha broder full#
Thankfully, none of the exposed employees contracted the virus, and the infected employee made a full recovery. The Outcomeīy the end of the first day, the VP of Operations and IT Technician had learned the Pacejet solution and took over through the rest of quarantine.

Alphabroder|Prime attributes Pacejet’s thorough implementation and backend set up as the foundation for the flexibility and ease-of-use they experienced during this challenging time. The remote shipping team processed orders using Pacejet’s web-based platform while the makeshift staff onsite weighed and labeled packages. Over the quarantine period, alphabroder|Prime’s VP of Operations and IT Technician continued order fulfillment. Because of this, alphabroder|Prime searched for a shipping solution that integrated with NetSuite, was cloud-based, and consolidated their shipping processes. Alphabroder|Prime also had many workstations with specific shippers trained to man certain stations. Before, alphabroder|Prime used various platforms, solutions, and portals to ship products to customers, along with different licenses for each shipper and translation tools for the ERP. Without Pacejet, business continuity would not have been possible. Thankfully, alphabroder|Prime had already streamlined their shipping processes with Pacejet, and the quarantined shippers processed orders remotely while the new two-person team sorted, packed, and executed all shipments. These employees were the VP of Operations and an IT Technician, both of whom had zero shipping experience and no familiarity with the Pacejet solution or alphabroder|Prime’s processes. Luckily, alphabroder|Prime implemented Pacejet a few months before, and used the cloud-based functionality to keep shipping processes online.Īs alphabroder|Prime entered crisis mode, they only had two employees available to fulfill onsite shipping requirements. This included the entire shipping staff of more than 10 people in their Connecticut location, leaving the company with no time to find alternative staffing resources. Despite practicing stringent social distancing, alphabroder|Prime quarantined anyone with possible exposure. Keeping up in Crisis Modeĭuring the COVID-19 pandemic, one of alphabroder|Prime’s employees was unknowingly positive for the virus while at work. With four different hard goods locations throughout the nation, alphabroder|Prime fulfills orders within the United States and internationally. Alphabroder|Prime supplies their network of distributors and promotional agencies with a catalog of items and ships products directly to end-users. They ship and imprint hard goods such as pens, mugs, notebooks, and other custom items for ad specialty distributors. Founded in 1980, alphabroder|Prime is a large supplier within the promotional products industry.
